Kevin’s Blog / SAGD short stories:
From Bitumen to Sales Oil
“SAGD short stories” is a blog series about SAGD and process operations.
If you’re interested in how the Steam Assisted Gravity Drainage (SAGD) heavy oil recovery method delivers crude oil at Sales Oil specifications, this article highlights most of the process covered in detail in our SAGD Training Course.
SAGD Oil Sands Production – From Bitumen to Sales Oil
In today’s short post we will be taking a bit of time to go over the SAGD Extraction Process and in particular how the SAGD Wells produce a mixed emulsion of bitumen, hot water (from condensing steam), some solids (mostly sand), and natural gas. From there, to produce Sales Oil, the bitumen has to have nearly all of the other components removed. This post summarizes the process but our full course details exactly how this is achieved.
Basic SAGD Challenges & Solutions
Explanations of emulsions and the separation of gas, oil and water phases allow our students to understand the basic challenges and solutions involved with SAGD production. We also explain how emulsion breaker chemicals are used to enhance the separation process.
During the phase separation discussion, API gravity and the API Gravity scale, as well as density adjustment, are explained. How Diluent is used as a diluting agent for density adjustment of the bitumen stream is also explained.
Free Water Knock Outs & Treaters
This process is actually pretty simple in concept, and relies on established engineering principles, such as pressure and temperature manipulation to cause certain reactions. It requires very specifically designed equipment, especially the Free Water Knock Out (FWKO) and Treater.
A FWKO is a large 3-phase separator that allows free water to simply separate out of the emulsion by gravity, as gas breaks out into the vapour space.
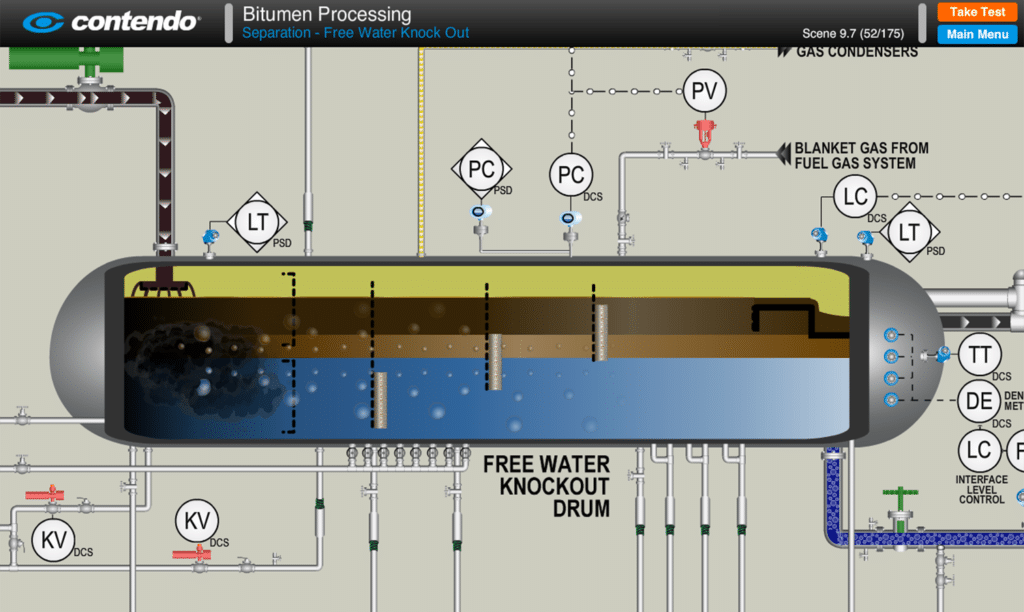
A Treater is also a large 3-phase separator, but is designed to handle a stream containing lower percentages of water and gas. Simple gravity separation Treaters rely on baffles or other internal structures encourage water droplets to coalesce and drop out of the hydrocarbon stream passing through the vessel.

A more complicated type is the Electrostatic Treater. It has an internal electrostatic grid system for removal of finer droplets of water through the application of electrical current (DC). Both Produced Water and Produced Gas are directed out of these vessels to dedicated systems.
Flowing the Bitumen Stream
An interesting topic is how the density of the bitumen stream is manipulated as it is moved through the process. In the ground, the naturally occurring bitumen is mixed with sand and appears more solid than liquid. It only flows out of the ground because its density is lowered in the downhole steam chamber by heating and mixing with water to make a liquid emulsion. The bitumen-emulsion density stays the same until the FWKO removes a large percentage of its water phase. The bitumen-emulsion leaving the FWKO only flows because it is still hot enough. If allowed to cool, the bitumen density would increase past the point of being easily pumped. By adding a hydrocarbon liquid diluting agent, an acceptable density is m maintained even after cooling to storage temperatures downstream. (Note: Bitumen diluted with Diluent or Synthetic Crude is commonly referred to as Dilbit or Synbit.
Two major operational points concerning the emulsion separator vessels is the development of a rag layer (‘rag’) between the ‘clean’ oil and the ‘clean’ water, and the accumulation of sand and other solids that drop out of the liquids.
SAGD Slop Handling
The rag layer is made up of unbroken emulsions that collect between the oil and water phases. The rag layer develops and becomes thicker over time, making it progressively harder for the oil and water phases to travel through it. The course explains how vessel design and operating practices enable removal and re-processing of the unbroken emulsions that make up the rag layer in the Slop Handling section.
The accumulated sand, etc. is removed from the FWKO and Treater using dedicated desanding equipment built into the vessels. The removed sand, etc. is then directed to a Desand Tank for depressuring, settling and eventual disposal.
Other modules are dedicated to handling low-pressure tank vapours in the Vapour Recovery Unit; handling gas and liquid PSV relief events; handling and processing high-pressure Produced Gas into fuel gas; Flaring operations; and Fuel Gas supply systems.
To find out more about how bitumen is processed to sales oil in a SAGD facility,
you can view the various chapters of Contendo’s SAGD Oil Sands Online – Bitumen Processing Course.
Kevin Fox is a senior technical writer at Contendo.
He is a power engineer who has written process education programs for industrial clients since 2009.
To Learn More
At Contendo, we have been providing in-depth online operator training to the Oil Sands and SAGD industry for the better part of a decade. If you want to learn more about this complex but highly efficient extraction method, stay tuned for more posts like this or contact us to hear more about our SAGD Oil Sands Online Training Course.
Was this article helpful? We’d love to keep in touch with you. Click here to sign up for our online newsletter.