Kevin’s Blog / SAGD short stories:
Gravity and Density
“SAGD short stories” is a blog series concerning SAGD operations.
While the SAGD process requires a large energy investment in steam production, one of the main downstream process functions doesn’t require any additional energy input.
In various vessels and tanks in a SAGD facility, gravity is the main driver of the process; specifically, how gravity acts on substances with different densities.
Most everyone has seen a mixture of oil and water, and regardless of whether the “oil” is gasoline shining on a puddle at the gas pump, or “grease” in the dishwater, the oily part is essentially floating on the water because it is less dense than the water, despite sometimes being more viscous than water.
The mixed emulsion of bitumen, gas, water and sand produced in SAGD is transported at a high enough pressure and velocity to maintain the emulsion, and this is important in inhibiting separation of the emulsion in the pipeline.
Once the emulsion reaches the processing facility, however, we want to progressively break down the emulsion into its component parts through pressure and flow manipulation, with as little energy expenditure as possible.
The entire emulsion is fed into a Free Water Knock Out drum (FWKO), which is a “gravity separator” that performs two main process actions:
-
First, it really slows down the flow velocity, because it is huge! This is a common trait of gravity separators, which causes the emulsion to stay in the vessel for a significant time period. Slow, non-turbulent flow lets the heaviest, most dense substances, like sand, fall out of suspension and sink to the bottom, and the lightest, least dense substances, like hydrocarbon gases, to rise to the top.
-
Second, because it is operated with a controlled liquid level (dictated by the height of an overflow weir) and at a lower pressure than the supply pipeline, it allows the substances with the lowest densities to not only rise to the surface of the liquid but to completely break out of the emulsion liquids into the vapour space provided by the level control.
The size of the separator provides enough retention time for the emulsion to mostly separate into a lower ‘oily water” layer and an upper “watery oil” layer.
By providing 4 separate outlets, a gravity separator can:
-
Vent the gas/vapour space to the Produced Gas handling system
-
Draw off the “oil” layer to the Bitumen Processing system
-
Draw off the “water” layer to the Produced Water De-oiling system
-
Periodically flush accumulated sand to the De-sanding system
By repeating this low velocity / high retention operating model in various gas and liquid processing vessels and tanks, gravity separation is utilized throughout the SAGD process.
While this is pretty straightforward, I haven’t included a major SAGD reality – we are recovering bitumen.
Bitumen is much more dense than the crude oil transported in pipelines, and can even be more dense than water! Bitumen is also very viscous; in fact it can appear as a solid at room temperature. Remember, we have to heat it and mix it with hot water to get it to the plant. When we remove the “hot” and the “water”, it’s just regular bitumen again.
When the bitumen is near the same density as water, gravity separation is much less efficient, and if the bitumen is too viscous it is impossible to pump. These issues are mitigated by density adjustment of the bitumen component with a diluting agent called diluent, which is a light, low-density hydrocarbon liquid.
Diluent is the “grease” that keeps the SAGD Bitumen Processing train moving.
Without it, the bitumen doesn’t flow. It’s that simple. Most facilities refer to their bitumen stream by names like Dilbit or Synbit, shortened forms of diluent and bitumen blend or synthetic diluent and bitumen blend. I’ll use Dilbit from here on.
Diluent added to the emulsion naturally mixes with the bitumen, as both are hydrocarbons; reducing the overall density of the Dilbit and increasing the density difference between the Dilbit and the water. A large density difference improves the separation efficiency, producing cleaner Dilbit and Produced Water discharge streams.
As each of these streams progress through their respective processing trains, gravity separation is used at least in part in a majority of the systems.
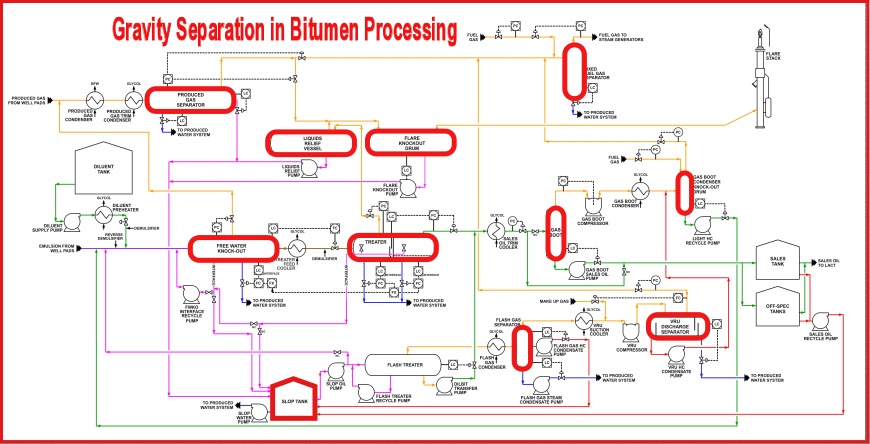
Vessels or Processes using gravity separation in Bitumen Processing include:
- Free Water Knock Out Drums
- Treaters
- Skim Tanks
- IGF Units
- Produced Water Tanks
- De-Oiled Water Tanks
- Slop Tanks
- Recycle Tanks
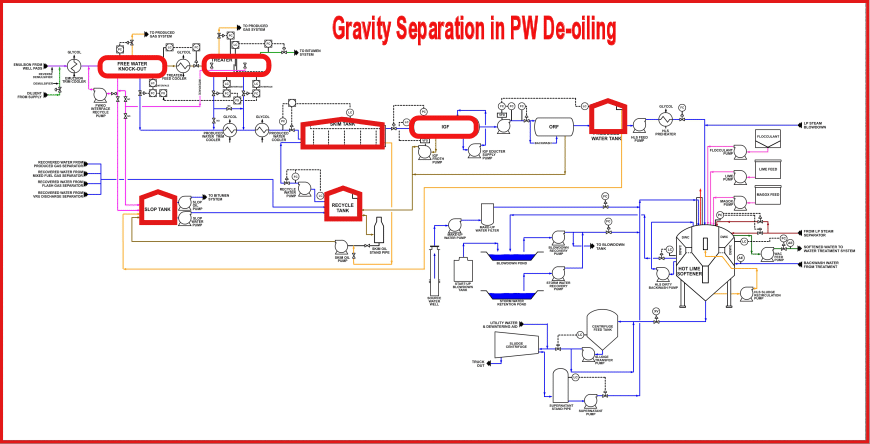
Vessels or Processes using gravity separation in Produced Water De-oiling include:
- Free Water Knock Out Drums
- Treaters
- Skim Tanks
- IGF Units
- Produced Water Tanks
- De-Oiled Water Tanks
- Slop Tanks
- Recycle Tanks
The last point I’d like to discuss about gravity separation is that an interface layer, or “rag layer”, usually forms between the Dilbit and water layers in gravity separator pressure vessels (and sometimes forms in process tanks). This rag layer is made up of unbroken emulsion with an overall density that places it between the Dilbit and water layers. If allowed to overdevelop and thicken, this rag layer can seriously impede migration of oil and water droplets through it and reduce the efficiency of the process.
This is solved by vessel design, which should allow sampling and testing to see the profile of the process, including the quality and thickness of the rag layer, and provide a means for drawing off the rag layer for recycling without removing the vessel or tank from service.
When combined with other mechanical or chemical treatments, gravity separation makes up a major part of the various methods of removing water, sand, and other contaminants from bitumen.
To find out more about the Gravity Separation and density adjustment,
you can view the Separation and Diluent chapters of Contendo’s SAGD Oil Sands Online – Bitumen Processing Course.
Kevin Fox is a senior technical writer at Contendo.
He is a power engineer who has written process education programs for industrial clients since 2009.
To Learn More
At Contendo, we have been providing in-depth online operator training to the Oil Sands and SAGD industry for the better part of a decade. If you want to learn more about this complex but highly efficient extraction method, stay tuned for more posts like this or contact us to hear more about our SAGD Oil Sands Online Training Course.
Was this article helpful? We’d love to keep in touch with you. Click here to sign up for our online newsletter.