SAGD short stories
SAGD: Cap Rock’s second career
“SAGD short stories” is a blog series about SAGD and process operations.
An essential feature for SAGD bitumen production is a suitable cap rock, which creates a boundary for steam and isolates the high pressure from the surface. But cap rock has been a major player for much longer than we’ve been around. SAGD only takes advantage of it.
Without cap rock, migrating hydrocarbon fluids could have made it to the surface and been recycled into nature. Meaning, no Age of Oil!
Instead, cap rock held things in reserve.
Most oil is recovered from solid rock (the oil sands are generally unconsolidated sandstone). The oil is trapped in reservoir rock under the impermeable cap rock, which prevented natural migration of fluids to the surface.
What’s the difference between reservoir rock and cap rock?
All rock looks solid to the naked eye, but reservoir rock is really a porous material, with pores and gaps filled with fluids (water, gas, or oil). When enough of the pores are connected, the fluids can move through the rock.
The cap rock doesn’t have these pores and forms a seal around the source rock that traps the oil.
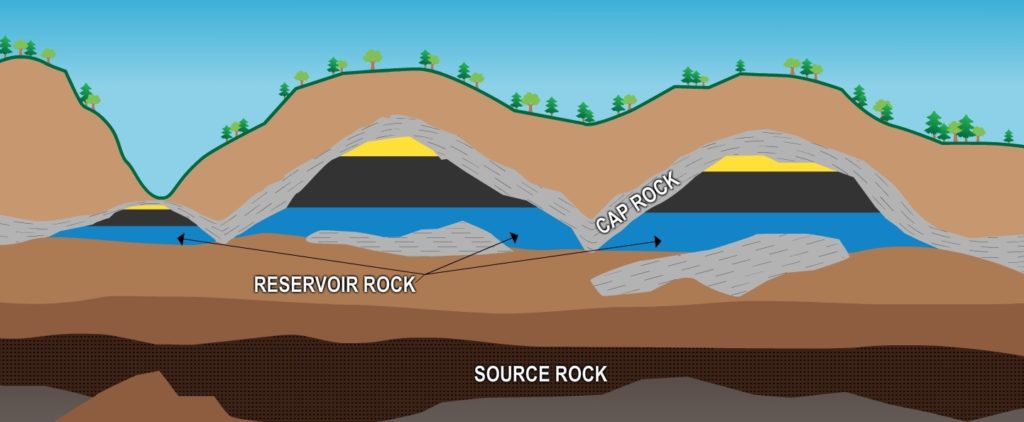
Reservoir Rock
Porosity and Permeability are measurable characteristics common to reservoir rock.
Porosity is the volume within the rock that can hold fluids, as a measurement of the pores. However, if the pores aren’t connected, then fluids can’t move through the rock. This means a rock’s effective porosity is only based on interconnected pores that support fluid flow.
Permeability can be looked at as a rock’s capacity to flow fluids through interconnected pores, or as a rock’s resistance to flow, when a differential pressure exists across the rock. A high permeability rock only needs a low differential pressure to move the fluid.
So, a good reservoir rock has high porosity to hold large amounts of fluids, and high permeability to efficiently flow fluids.
Examples of good reservoir rocks, such as limestone and sandstone, have permeability in the range of 100 to 10,000 millidarcys.
Cap Rock
A cap rock has such low porosity it is impermeable to fluids.
For example, a granite cap rock has a permeability of < 0.00001 millidarcy.
Permeability
reservoir rock = 100 to 10,000 millidarcys
cap rock < 0.00001 millidarcy
SAGD Reservoir Containment Seal
We often describe the oil as being “trapped” by impermeable cap rock, and the types of rock formations that make up reservoirs are actually called petroleum traps.
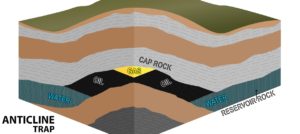
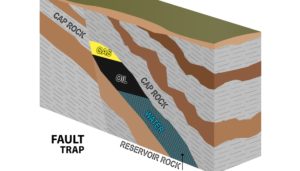
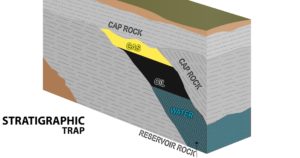
The sealing capability of the cap rock can be measured and evaluated by examining cores, borehole imaging, and other petrographic studies. The evaluation concerns the basic criteria for reservoir seal potential, which is Seal Integrity, Seal Geometry, and Seal Capacity.
Seal integrity describes how tight the seal is. It is the absence or presence of pathways, such as faults, fractures, and joints, which could let fluids pass. It relates to properties such as ductility, compressibility and propensity for fracturing.
Seal geometry describes the shape of the cap rock. It is the position, thickness and extent of sealing rock relative to the reservoir.
Seal capacity describes the amount of upward pressure the rock can withstand. It is the maximum hydrocarbon column height a seal can resist, which is a function of the relationship between the buoyancy pressure of the hydrocarbon column and the flow properties of the rock seal.
The SAGD process requires a cap rock that can withstand the added loads applied by the pressure of the injected steam. This requirement adds some complex calculations to the evaluation done by the Reservoir Engineering team.
Operating a “natural” pressure vessel
For a SAGD Well Pad Operator, the steam chamber zone under the cap rock is essentially a pressure vessel, except this one isn’t built of steel.
Instead of deciding on an operating pressure range and building a vessel to meet the need, SAGD requires a decision on the capabilities of the cap rock before any decision on operating pressure ranges are made.
For SAGD, the sealing capability of a cap rock is particularly critical where the cap rock is closer to the surface (less than 150m) or where the reservoir is close to important natural features, such as waterways, infrastructure or communities.
About 80% of Alberta’s total heavy oil reserve is buried greater than 75 meters and has potential for SAGD production. The bitumen lies in a layer approximately 20 to 60 meters thick that is up to 500 meters beneath the surface.
Not respecting the reservoir engineering operating recommendations and restrictions can result in the worst case scenario for a SAGD Operator, which is a failure of the cap rock and a breakthrough to the surface.
To find out more about how reservoirs and the Canadian Oil Sands were formed,
you can view the Reservoir chapter of Contendo’s SAGD Oil Sands Online – Well Pads Course.
Kevin Fox is a senior technical writer at Contendo.
He is a power engineer who has written process education programs for industrial clients since 2009.