[vc_row][vc_column][vc_column_text]
Kevin’s Blog / SAGD short stories:
Silent Security
“SAGD short stories” is a blog series about SAGD and process operations.
When looking at SAGD safety, I can’t think of a better topic than pressure relief and the silent security provided by mechanical pressure relief devices. These devices open at a specific pressure set point to relieve, or vent, excessive pressure to a safe location in order to prevent equipment damage or failure and injury to personnel. Every process system or piece of industrial equipment capable of creating pressure must be equipped with pressure relief capability.
Now, you may only be thinking of devices meant to relieve hazards posed by excessively high pressure, but some relief devices are meant to relieve excessively low pressure (vacuum). This is because it isn’t the absolute pressure contained, but rather the “pressure differential” between the interior and exterior of the containing piping, vessel, or equipment that poses the hazard.
The higher the differential pressure, the higher the hazard
posed by an uncontrolled release of the greater pressure.
Consider a diver’s SCUBA tank:
If the tank contains air at 2 times atmospheric pressure (a 2 bar internal “environment”),
but is at a depth of 10 meters (in a 2 bar external “environment”),
would a pressure release caused by a tank rupture be as violent as it would be at the surface?
Of course we do most of our industrial operations with atmospheric air pressure on one side of the pressure containing equipment, opposite the process pressure. Modern relief devices include pressure safety valves (PSV), pressure relief valves (PRV), vacuum relief valves (VRV), and combination pressure and vacuum relief valves (PVRV), as well as burst or rupture disks. Most of the relief valves have some kind of adjustment for setting the opening pressure, and are reusable after relief events. Rupture disks are manufactured to open (rupture) at a specific pressure and are single use devices.
Now we’re cooking!
When I looked into the history of the ubiquitous pressure relief valve, it wasn’t all that surprising to find out the first versions were concerned with cooking. What was being cooked was the surprise!
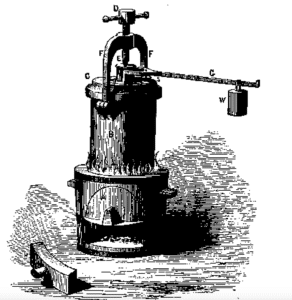
It was around 1680 when the first pressure relief device was fitted to “Papin’s Bone Digester”, a pressure cooker invented by Denis Papin to create “delicious meat jellies” from animal bones. This transformed the pressure cooker from a potential bomb into a relatively safe, reliable appliance anyone could use. As the reliability and design of the cooker and relief device were improved, higher cooking pressures were possible. Other uses were soon developed for the softened animal bones, including confections and dyes, and in chemistry.
The first pressure cooker soon led to other pressure vessels, such as autoclaves and hot water heating boilers, and instigated the evolution to steam boilers for driving pumps and engines, and to steam plants for heating, industrial or power generation purposes. All because of the safety and reliability afforded by an evolving array of pressure relief devices.
Would you have believed all of today’s high-pressure operations (steam or otherwise) sort of started with a desire to make meat jellies from animal bones without the danger of blowing up the cooker?
To find out more about SAGD and operating in the Canadian Oil Sands,
you can check outContendo’s SAGD Oil Sands Online Courses.
Kevin Fox is a senior technical writer at Contendo.
He is a power engineer who has written process education programs for industrial clients since 2009.
To Learn More
At Contendo, we have been providing in-depth online operator training to the Oil Sands and SAGD industry for the better part of a decade. If you want to learn more about SAGD or process operations, stay tuned for more posts like this, or contact us to hear more about our SAGD Oil Sands Online Training Course.
Was this article helpful? We’d love to keep in touch with you. Click here to sign up for our online newsletter.