Canadian Cutting Edge Oil Sands Research
The Canadian oil sands energy sector has a great record when it comes to the continuous development of innovative oil recovery technologies and methods.
So much so, it can be hard to keep up with all the ideas being worked on.
One of the most successful methods currently in wide usage is the SAGD thermal recovery process. SAGD stands for steam-assisted gravity drainage, which is an energy intensive method of injecting high-pressure, high-temperature steam into a highly viscous pay zone of bitumen-laden oil sands and recovering a bitumen emulsion. This emulsion is a mixture of hydrocarbon liquids, natural gases, and hot condensate water (from steam), as well as fine solids and sand.
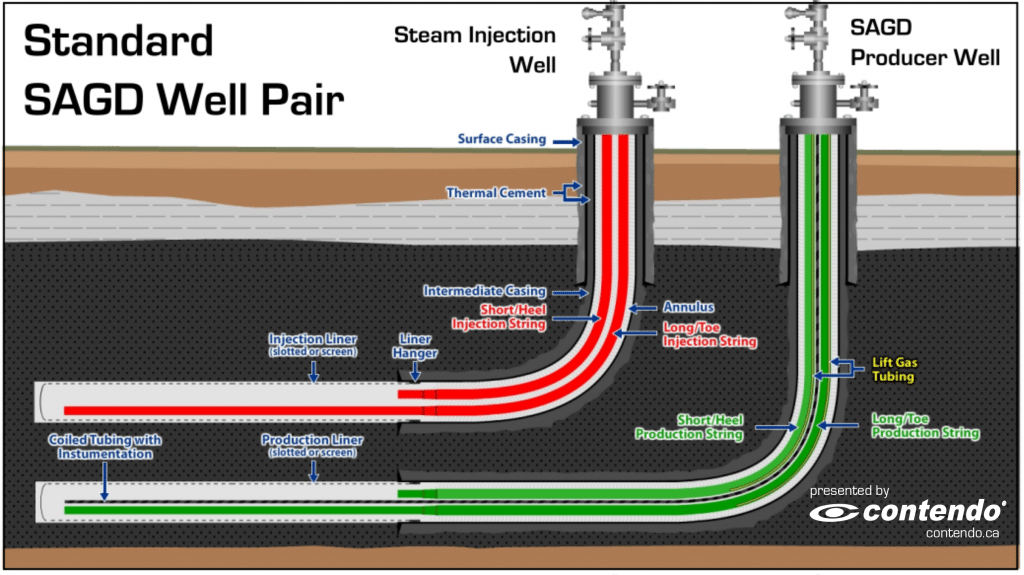
EOR (enhanced oil recovery) methods used in conjunction with SAGD include adding various solvents to the injection steam, increasing production rates to the surface with downhole submersible pump and gas lift technologies, and cyclic operation practices. Cutting edge developments in heat recovery and electrical cogeneration boiler operations are being included in the next generation of facility design and construction. Progress is being made in proving the potential and reliability of direct-contact steam generation (DCSG).
However, up to now, every concept touted as the next big development in SAGD has been based on injecting high-pressure steam into the reservoir.
But then somebody somewhere had to ask a radical question:
Can a SAGD process be designed to operate without injecting steam?
It turns out this may be possible, and testing is scheduled for 3rd quarter 2019 to investigate the use of electromagnetic energy to stimulate the pay zone and mobilize the bitumen for recovery. Here’s my simplified explanation how the process is intended to work.
SAGD is based on pairs of perforated well bores drilled in a horizontal, over/under arrangement at the depth of the pay zone. Steam enters the reservoir through the upper injection well, condenses to hot water as it warms up the oil sand and is recovered to the surface as part of the overall bitumen emulsion.
In the RF stimulation process, each Producer Well is drilled vertically to the pay zone before turning to horizontal and continuing for up to a couple of kilometers. The horizontal section is still perforated so fluids can enter and flow to the surface. The Producer Well still has a matching well bore drilled above it, but this one has an un-perforated steel pipe installed to act as a kind of transmission antennae.
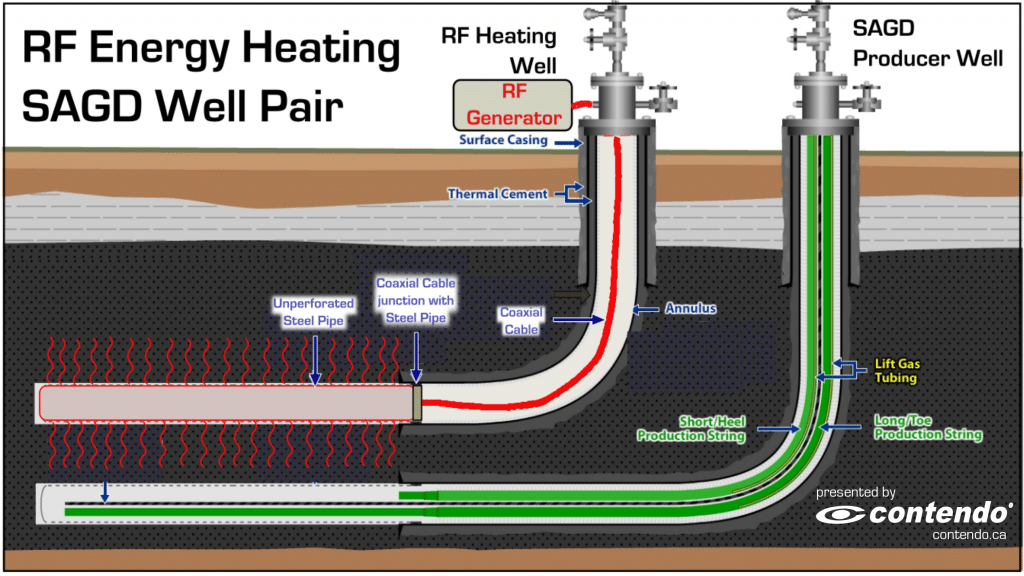
Electromagnetic energy, in the form of radio frequency, or RF energy, is produced locally at the well pad and transmitted downhole through coaxial cables inside a standard vertical casing to the horizontal section. Once past the heel, the coaxial cable connects to an open transmission line inside the steel pipe. The steel pipe acts as a lossy transmission line, which allows a strong transfer of energy to liquid water molecules trapped in the oil sands all along the horizontal pipe. In the same manner as a microwave oven, the energy excites the water and causes it to heat up until to converts to steam. From this point, the process closely mimics standard SAGD as the steam gives up heat to the pay zone to mobilize the bitumen, which drains to the lower producer well.
I’m blown away by the possibilities.
RF Heating using an affordable, efficient RF energy generator located at a well pad only requires an electrical power supply. A regular Emergency Generator with switchgear could keep the well pad producing through short term power interruptions.
This would replace complex pipeline systems for high-pressure steam supply and condensate recovery, and eliminate well pad production losses due to problems in those systems.
The size of production vessels could be reduced, as only reservoir water is brought to the surface with the bitumen. In fact, a lot of the SAGD-style processing system would be eliminated, with no produced water de-oiling and recycling to boiler feed water at all.
I can see applications for RF Heating in downstream process vessels and storage tanks. In SAGD, light hydrocarbon fluids called diluent are added to dilute the bitumen at each step where produced water is removed, in order to maintain flow properties as the bitumen cools. RF Heating at the storage tanks could keep the bitumen-water mixture mobile with minimal diluent addition. The reduced volume being transported would see a significant saving in cost, as would a reduction in the amount of diluent needed.
I can even imagine a super high tech railway car equipped with RF Heating capability. Loading bitumen hot, rather than diluted, would get more profit (bitumen only) in each car. At the receiving facility, cars queued for unloading could be pre-heated to the desired temperature while in line for the unloading station. If we equip the rail car wheels with electrical generation capability along the lines of hybrid car regenerative braking, we have a basically free heating circuit during transport. This would let us keep the bitumen at a temperature and pressure that permits flow without an excessive release of gases.
This RF energy technology is a potential game changer with applications across all heavy oil production methods, but especially thermal recovery methods. If we can replace proven steam heating reservoir stimulation methods with electricity-based RF energy stimulation, we can eliminate the entire SAGD steam generation plant and water inventory. With no boiler flue gas emissions or fresh water requirements, the environmental impacts of oil sands development will be greatly reduced.
Kevin Fox is a technical writer at Contendo. He is a power engineer with a background in process operations, steel fabrication and military.